Our service
Modules undergo a full inspection including stripping back of any coatings in damaged areas to inspect the material core; a review of all metallic inserts to check for damage, breakage or corrosion; overall inspection of the modules checked against the original specifications including weight in air and weight in water calibrated testing; and a dimensional laser scan. Â
We then produce an in-depth report showing the extent of necessary works and a full scope of works detailing the required actions to bring them back to operational standard.
Modules are assessed depending on the level of damage/wear and recommendations are given for the specific repairs required for the system and the associated costs and timescales. Any modules that are deemed beyond repair are identified with details of any fundamental failures documented. Â
Talk to us about your requirements for expert advice and reccomendations
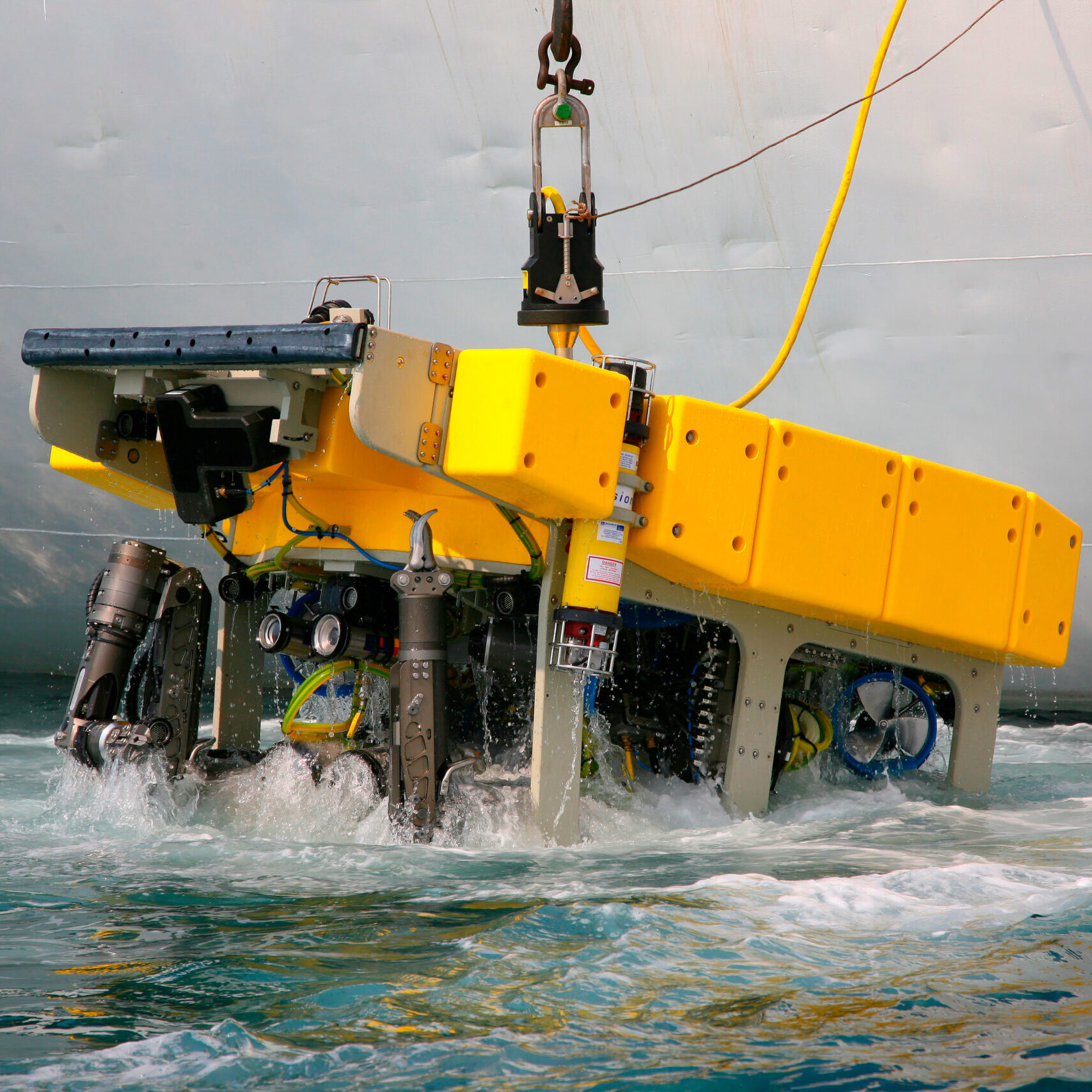
What's included
- Repair of any scuffs, cracks, splits and chips Â
- Replacement of any missing sectionsÂ
- Repair of damaged edges Â
- Replace any damaged insertsÂ
- Incorporation of new additional inserts Â
- Repaint or a change of paint colour (marine grade)Â
- Recoating with a fresh PU or GRP skin to improve longevity for abrasion and impact resistanceÂ
- Application of any logos, stencil graphics or nonslip coatingsÂ
Â
Key Features
As part of our subsea buoyancy repair and refurbishment service, all works are completed using approved materials and processes and finished to industry-recognised standards. Our complete range of materials has DNV approval of manufacture, and our 11500 depth-rated material has DNV type approval. We provide all work undertaken with a 6-month warranty, giving you peace of mind. Â
Along with your ‘as new’ modules, you receive a final documentation package which includes: an overall certificate of conformity, buoyancy certificates, dimensional laser scan report, and material certifications for any syntactic foam or metallic inserts used. Â
Should refurbishment not be an option, we will work with you to find a cost-effective solution for a brand-new module.Â
The initial inspection is a fully chargeable service based on the size and quantity of the modules being assessed. An estimate can be given for the cost of repairs using video and photographic evidence; however, an accurate quote cannot be provided until the full inspection work is complete. Â
After the inspection, you can choose whether to go ahead or not. There is no obligation to proceed with the recommended repairs. Â
"The buoyancy models you supplied look superb. One of the best finished we've ever seen!" Matt, Forum Energy Technologies
BENEFITS
- Extended service lifeÂ
- Ensuring maximum usage and return on investmentÂ
- More cost-effective than a new set with a quicker lead timeÂ
- Allows you time to plan for a replacement set whilst still using the ROVÂ Â
- Opportunity to change paint colours or change or add stencillingÂ
- Opportunity to make modifications, for example, add a bigger camera; add buoyancy; change the lighting configuration; or change the mounting configuration Â
- Reducing waste to landfill Â