Widely used in manufacturing and engineering processes, modelling and tooling boards are engineered to support the creation of highly accurate prototypes, patterns and mould tools, and for styling, modelling and specialist applications in industries including aerospace, automotive, advanced manufacturing, and foundry.
Modelling and tooling boards are available in a variety of materials, each offering unique properties suited to different manufacturing applications. When selecting the type of board for a project, it's important that the specific needs of both the application and process are understood. Selecting the right material ensures it is fit for purpose, provides optimal production efficiency, and results in a high-quality final part.
For instance, a low or medium-density polyurethane (PU) modelling board offers a cost-effective solution for prototyping projects where visual design replication is required, through to vacuum forming, thermoforming, and the manufacturing of jigs and fixtures. High-density polyurethane materials are specifically engineered for more specialist applications, including hammer and metal forming, foundry patterns, and Reactive Injection Moulding (RIM) tools where toughness and durability are key.
Whereas an epoxy tooling board is used in all forms of carbon fibre production, including the manufacture of prepreg composite tooling. Designed for applications where temperature and pressure are key considerations, for example, aerospace and automotive patterns and moulds for short-run direct-to-part manufacturing. Epoxy tooling boards boast a low CTE and when combined with a toughened resin matrix, provide a durable material for use at elevated temperatures in an autoclave. When used with carbon fibre prepregs, the inert surface of an epoxy tooling board ensures there is no negative interaction or inhibition as can be seen with PU, Hybrid and other isocyanate-cured products.
Selecting the right solution
A key factor in the choice of a tooling board is the thermal properties of the material. The temperature resistance and the Coefficient of Thermal Expansion (CTE) often play a crucial role. Tooling boards with a low CTE experience less expansion as temperatures increase, ensuring consistent and precise results. Additionally, the surface structure of the board is directly linked to the surface finish of the final part, and a finer surface will ultimately reduce the processing effort required. Selecting the right sealing solution for the chosen board material is also an important consideration, as is the application method for the sealer itself. By carefully considering these physical properties, manufacturers can select the optimal solution to enhance precision, efficiency, and the overall success of a project.
In addition to performance considerations, it's important to also think about the environmental impact of the materials you choose. Traditional alternatives such as medium-density fibreboard (MDF) bonded with formaldehyde or phenol-formaldehyde, which are known cancer causing carcinogens, have often been used as a cost-saving option. Opting for modelling and tooling boards with bio-based raw materials and recycled content can help reduce the demand for MDF, supporting more environmentally friendly manufacturing practices and lowering reliance on fossil-based raw materials. This is a key consideration for businesses seeking to align with sustainability goals and reduce the environmental impact of their operations.
Compromising quality for cost
Sometimes chosen for low-budget projects, alternatives, including MDF or low-density foam, are used for projects with minimal details or simple geometry. However, their suitability as a tooling material is compromised by several factors including performance and longevity.
Another key concern is bonding, as MDF absorbs moisture and will swell, leading to inconsistencies in the bonding process and weakening of the pattern over time, even with moisture-resistant variants. Surface profile deterioration is another known issue. Some materials can degrade over time, and during repeated use, this can lead to a rougher finish and the need for frequent maintenance or replacements. This becomes particularly problematic when repeatability is crucial, as the material's limited resistance to wear and tear can impact the ability to reuse patterns, unlike more durable tooling board alternatives, which retain their shape and finish over a longer period and through repeated use.
While low-cost alternatives may seem like an affordable choice upfront, it can ultimately be a false economy due to the increased labour and sealant required. In short, while they may be suitable for some simple, low-budget applications, the health risk should not be overlooked, and their limitations in terms of durability, surface finish, heat sensitivity, and overall performance make them unviable for more complex, precision-driven projects.
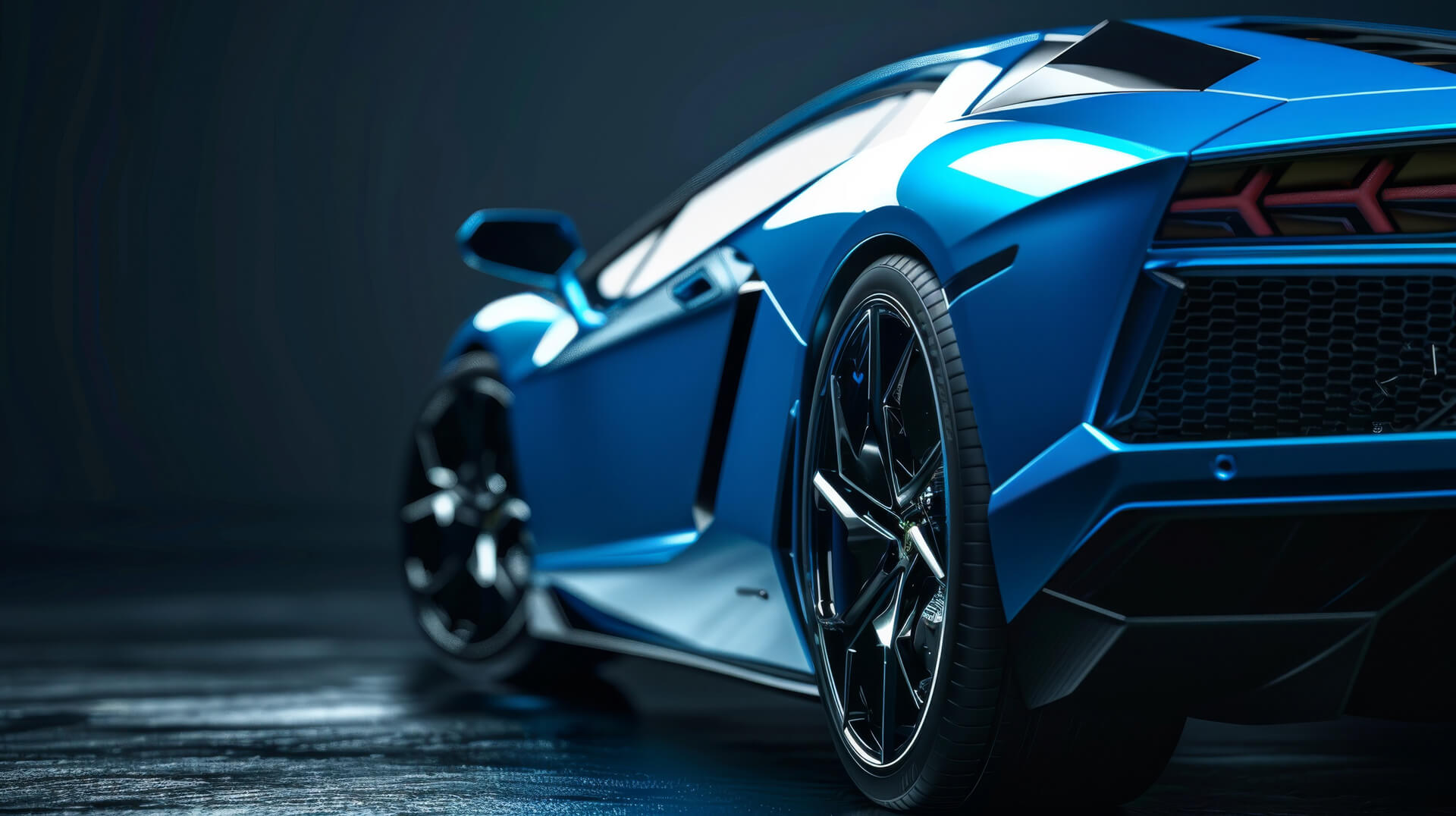
Making the case for PU
PU modelling boards offer significant advantages, particularly in terms of versatility, durability, and finish quality, whilst remaining cost-effective for budget-sensitive projects or where ambient temperature curing is a requirement. PU materials continue to evolve in formulation, with an ongoing increase in bio-based raw material content for improved environmental impact.
Whilst it is considered a lower-cost alternative to epoxy, due to its far-reaching applications, PU modelling boards are favoured for a wide range of applications, with low, medium, and high-density boards available for different project requirements. Lightweight, low-density boards provide a cost-effective solution for design, styling, modelling, and prototyping projects, while medium and high-density boards offer good dimensional stability and toughness, maintaining their shape through vacuum forming, thermoforming and foundry tooling processes.
Medium and high-density PU boards provide a good surface finish, offering a smooth, consistent surface that reduces the risk of defects in the final product. This is particularly beneficial for applications where the appearance of the end part is critical. Specially engineered high-density PU tooling boards offer additional properties like abrasion resistance to ensure that the tooling remains durable for repeat use or for the manufacturing of more specialist hammer and metal forming tools, foundry patterns, or foundry core boxes. With a wide range of densities available, PU board choice can be tailored to meet the specific needs of a project, making it a reliable, sustainable, high-performance, cost-effective solution for a broad range of applications.
The smarter choice for precision and durability
Ultimately, choosing the correct synthetic board material at the earliest stage in the design process will contribute to a higher-quality end product and a more streamlined, efficient production process. By selecting sustainable materials, companies not only enhance their production outcomes but can also contribute to a more environmentally responsible manufacturing ecosystem.
First published in Composites In Manufacturing Magazine, 2025.
OTHER NEWS
Sorry, we couldn't find any posts. Please try a different search.